About Nishijin-ori
About Nishijin-ori
Nishijin-ori is a traditional Japanese craft made in Kyoto, renowned for producing premium-grade textiles.
With a history dating back over 1,200 years to the Heian period, this intricate art form has been perfected and passed down by master artisans.
Recognized for its excellence by the Imperial Court, Nishijin-ori continues to symbolize the finest in Japanese textile artistry.
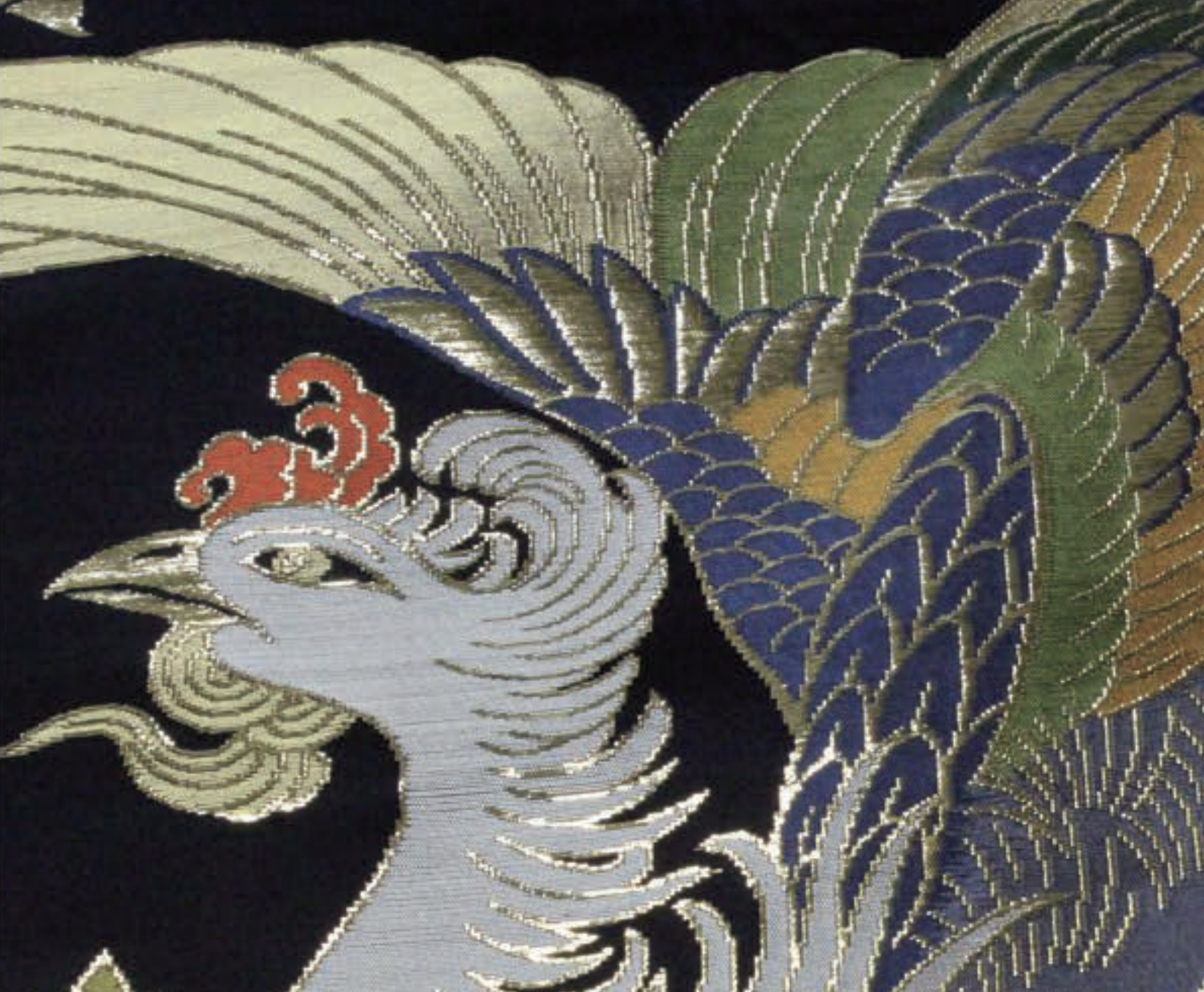
Nishijin brocade is characterized by its yarn-dyed patterned fabric, produced in small quantities across a wide range of varieties.
The production process is fundamentally based on a division of labor, encompassing numerous stages from planning and design to pattern creation, drafting, yarn dyeing, winding, warping, heddling, and gold and silver thread processing.
Each of these intricate steps is handled by specialized, skilled artisans, and only through the combined efforts of these craftsmen is a single piece of Nishijin fabric brought to completion.
Unique Features of Nishijin-ori
Nishijin-ori’s foundation lies in its dedication to craftsmanship.
Woven with high-quality silk and dyed threads, it merges traditional techniques with contemporary designs to create new forms of expression.
Artisans continuously innovate, crafting beautiful, trend-sensitive designs that captivate.
This meticulous attention to detail has earned Nishijin-ori its high reputation and enduring popularity.
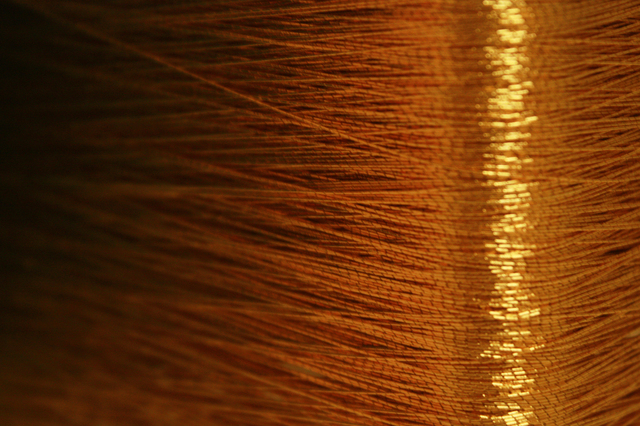
The Prestige of Gold Thread
Gold thread plays a key role in enhancing the luxurious quality of Nishijin-ori. The thread adds a shimmering, opulent effect to the fabric, evoking a sense of wealth and dignity. The radiant sparkle of gold thread under light creates a majestic, sophisticated look, elevating the brand's prestige.
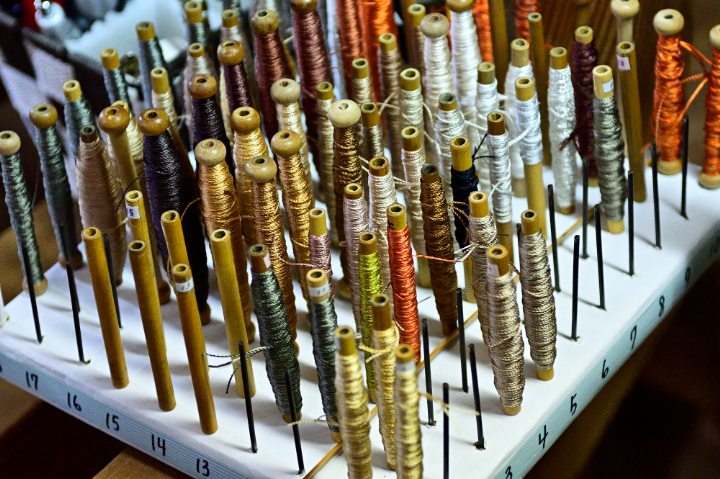
Pre-dyed Techniques for Distinctive Expression
The pre-dyeing technique of Nishijin-ori ensures its distinct texture and enduring beauty. By dyeing threads before weaving, the fabric retains its vivid colors and resists fading. The combination of colors in the threads creates unique depth and richness, allowing for a wide range of artistic expression.
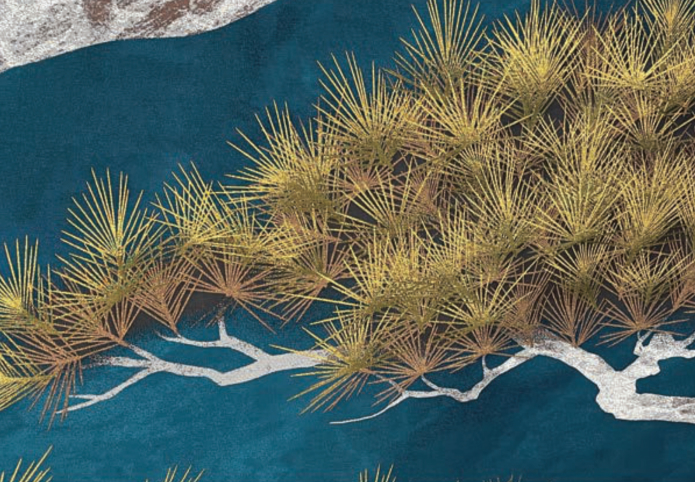
Versatile Weaving Methods
Nishijin-ori employs various weaving techniques, such as transparent fabrics and double-weaving structures. With 12 official types of Nishijin-ori recognized by law, each type offers its own distinctive weaving method and texture. For example, delicate fabrics like kinran (brocade with gold threads) are hand-woven for a highly refined finish, demonstrating the incredible precision and beauty of the craft.
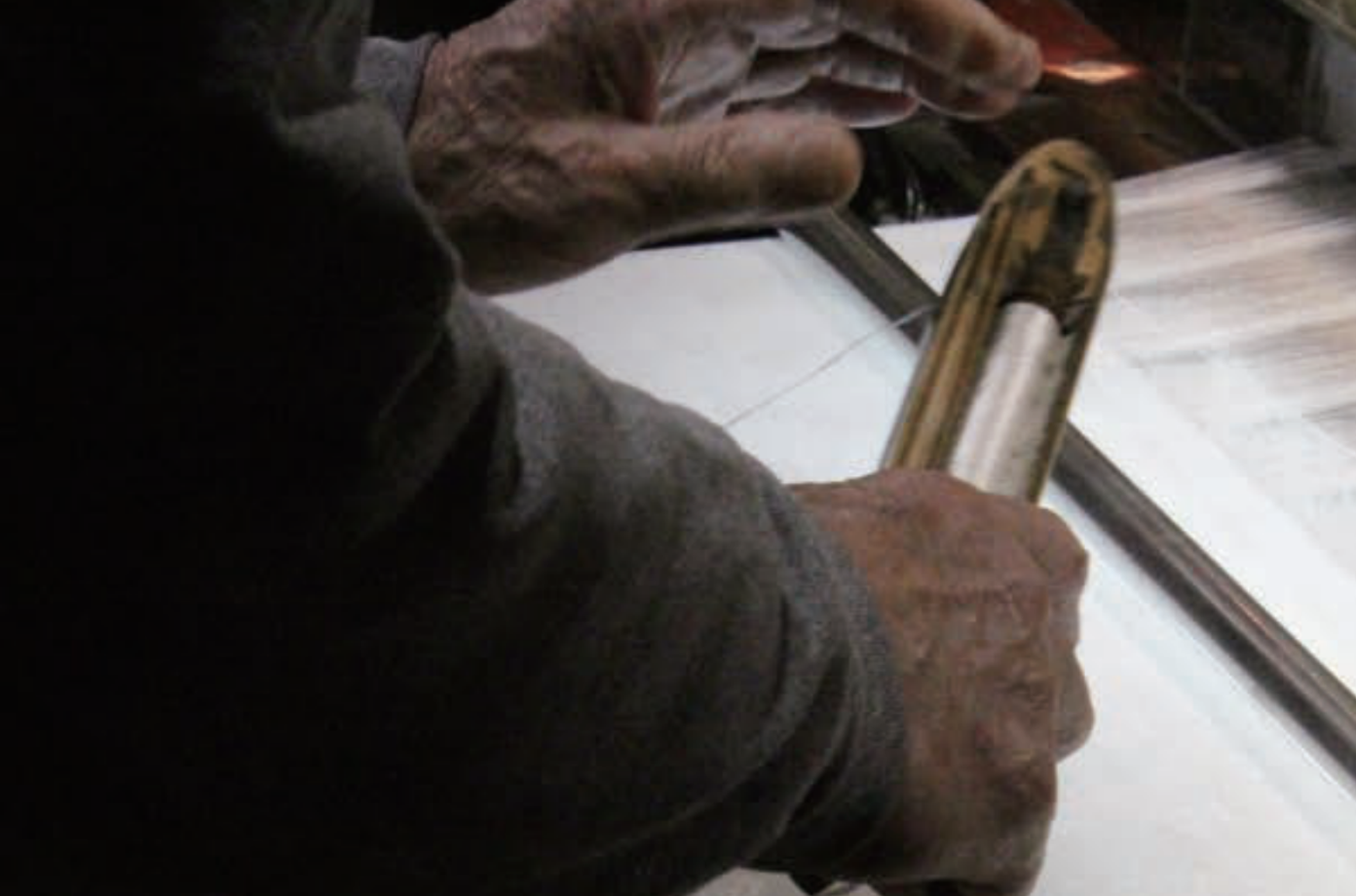
Luxury and Rarity
Nishijin-ori is a rare and valuable textile, made through a long and intricate process. Especially when hand-woven, the process can take several days to complete just a few centimeters of fabric. Each piece, woven meticulously by skilled artisans, is considered a high-end, exclusive work of art.
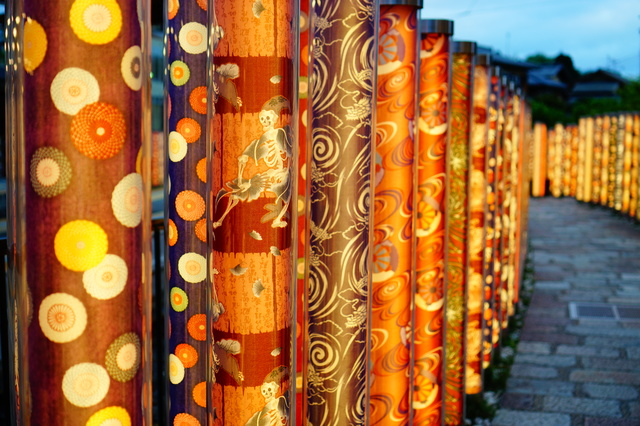
Infinite Design Possibilities
With the introduction of Jacquard looms, the design possibilities of Nishijin-ori have expanded significantly. This technology allows for the recreation of almost any pattern, and with access to over 500–600 silk colors, each piece can be tailored to match your exact vision. The extensive range of patterns and color options is one of the most alluring features of Nishijin-ori.
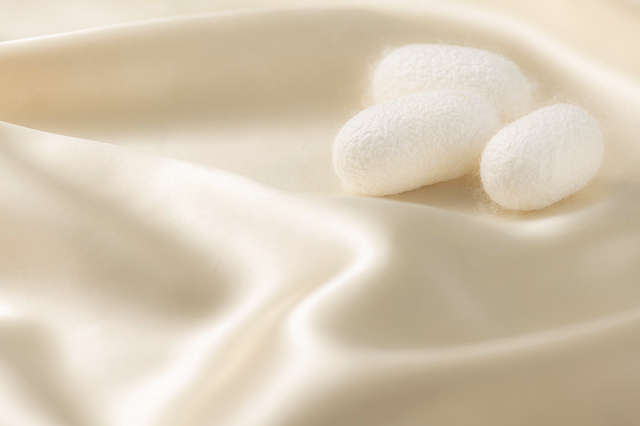
The Beauty of Genuine Silk
The silk used in Nishijin-ori offers a unique luster and vibrancy that synthetic fibers cannot replicate. The luxurious sheen of real silk provides an unmatched sense of elegance. Moreover, the distinctive “silk sound” produced by the fabric adds to its allure. This rich beauty captivates all who encounter it.
History of Nishijin-ori
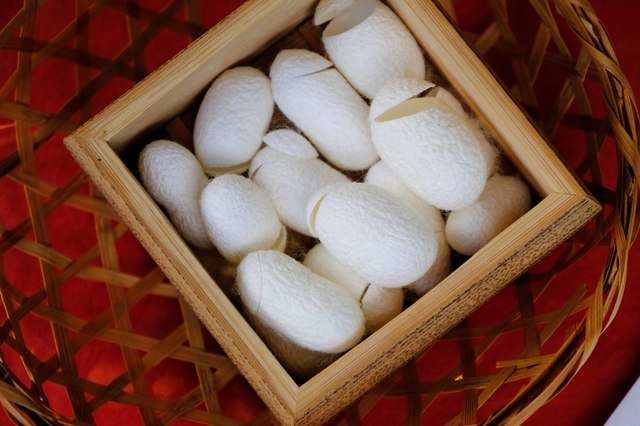
Origins
Nishijin-ori traces its origins to the 5th and 6th centuries when silk-weaving techniques were brought to Kyoto.
By the Heian period, the Imperial Court established a government-run weaving workshop known as "Oribe no Tsukasa."
Although the workshop eventually declined, Kyoto's weavers established independent workshops and continued to hone their craft.
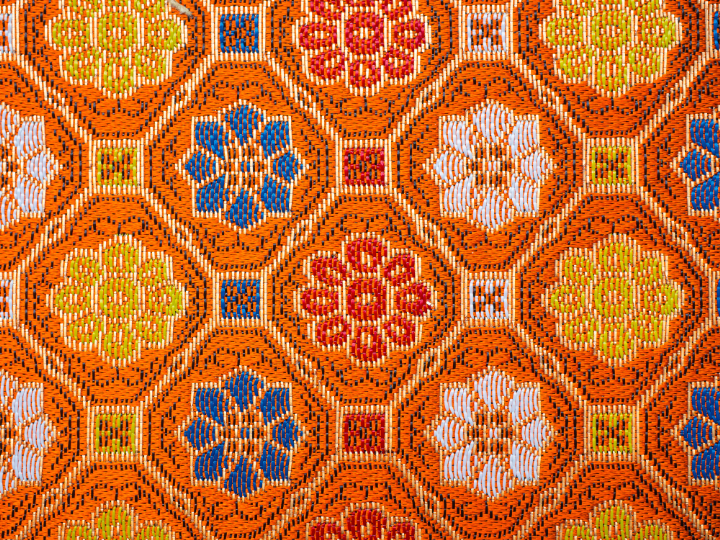
Revival During the Muromachi Period
During the Muromachi period, weavers formed a guild known as "Otoneri-za" in the Otoneri district, receiving commissions from the court, aristocrats, and warriors.
However, the Onin War destroyed much of Kyoto's weaving industry.
After the war, the artisans returned to the area called "Nishijin," and from there, the craft of Nishijin-ori was revived and named after the district.

Innovation in the Meiji Era
The Meiji era brought technological advancements with the introduction of Jacquard looms, revolutionizing the industry.
Nishijin-ori expanded beyond traditional kimonos to include interior textiles and Western-style products.
Today, Nishijin-ori is highly valued both domestically and internationally as a symbol of Japan’s finest silk weaving.
Manufacturing Process
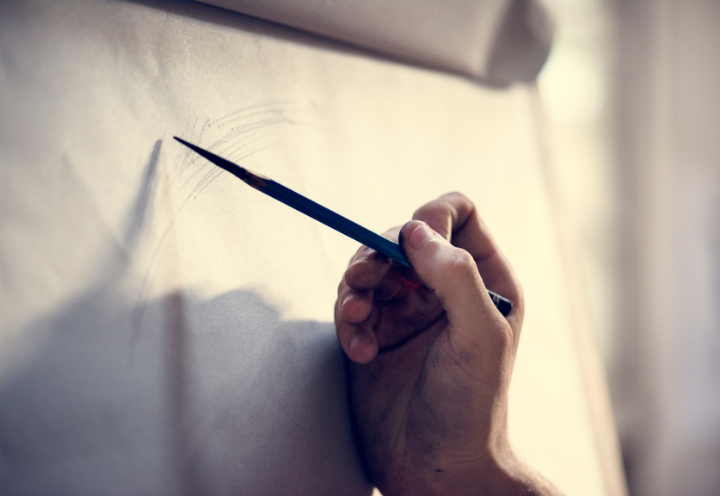
1.Design
Each piece of Nishijin-ori begins with a carefully crafted design, accounting for how the pre-dyed threads will be woven together to create the final image.
Designers incorporate both traditional and contemporary styles to meet modern demands.
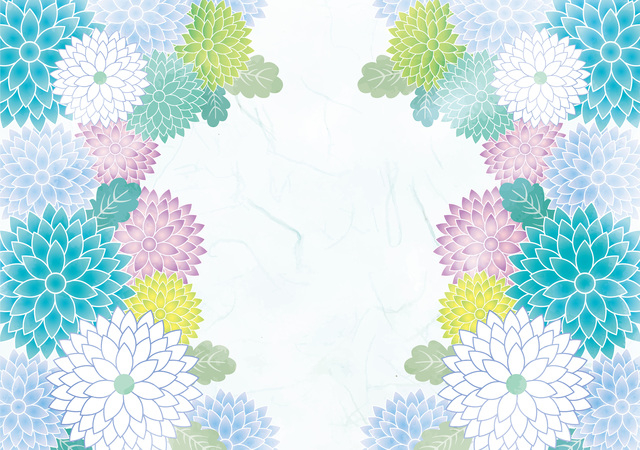
2.Pattern Drafting
Next, a detailed blueprint is created, instructing how the loom will manipulate the warp and weft threads.
This pattern is essential for achieving complex designs.
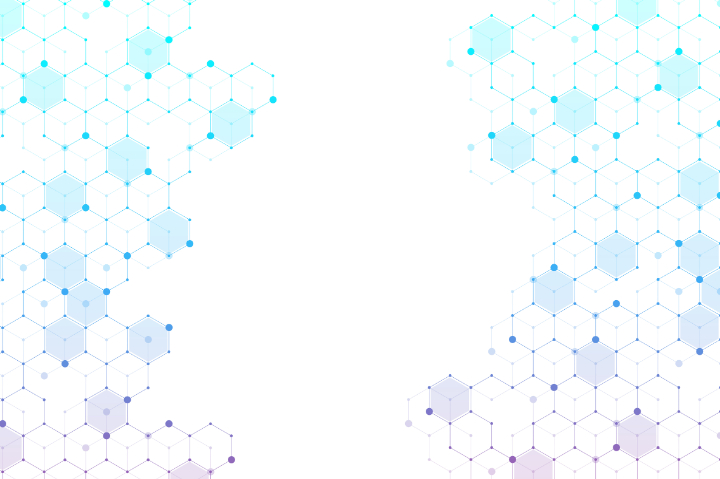
3.Punch Card Creation
Based on the blueprint, holes are punched into cards that direct the loom’s movements, ensuring the correct interplay of warp and weft threads to form the desired pattern.
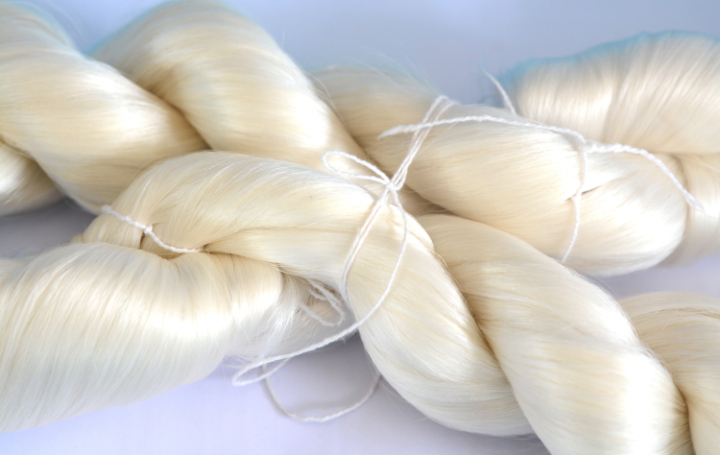
4.Twisting the Thread
To achieve Nishijin-ori's unique texture, raw silk threads are twisted together, creating varying thicknesses for different textures and finishes.
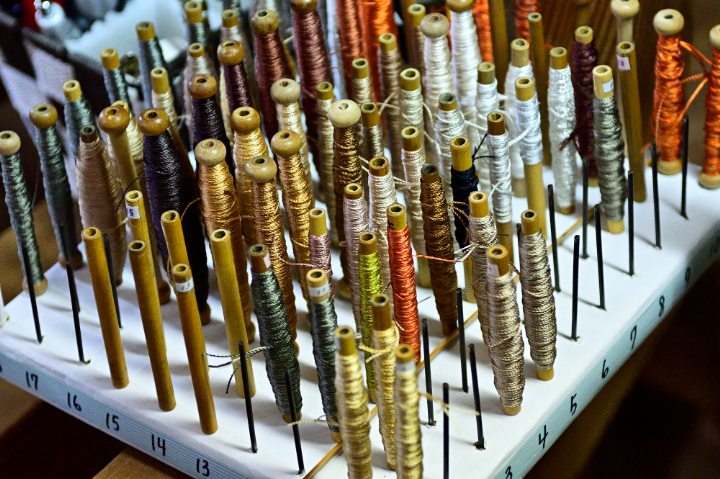
5.Dyeing the Threads
The white silk threads are dyed to the exact specifications required for each design, a process that significantly impacts the final product's look and feel.
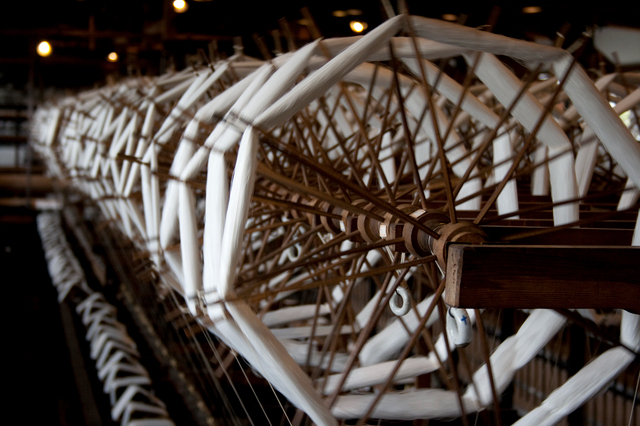
6.Thread Preparation
Both warp and weft threads are carefully prepared and wound onto spools, ready to be woven on the loom.
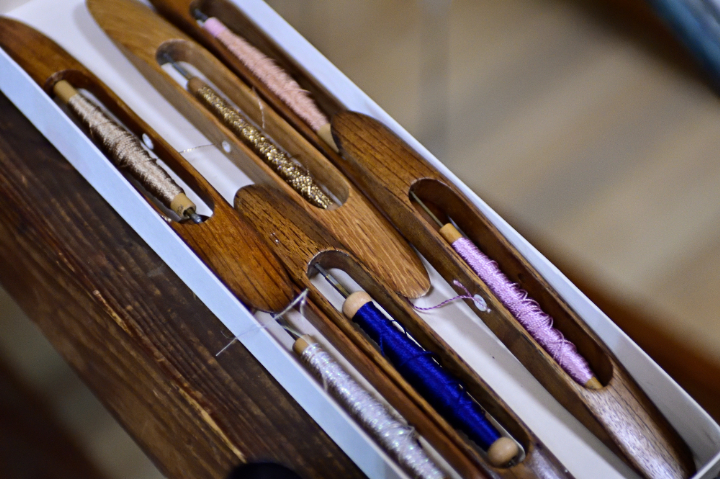
7.Warping and Weft Preparation
Thousands of warp threads are aligned, and the weft threads are wound onto bamboo spindles, setting the stage for the weaving process.
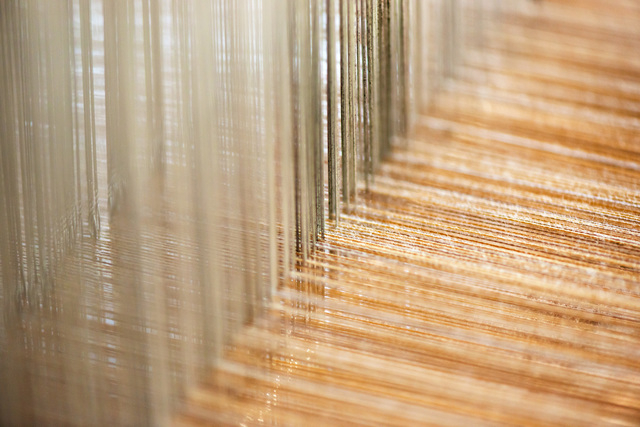
8.Harnessing the Loom
The loom is outfitted with a harness that lifts and separates the warp threads, allowing the weft threads to pass through.
This step is crucial for producing intricate patterns.
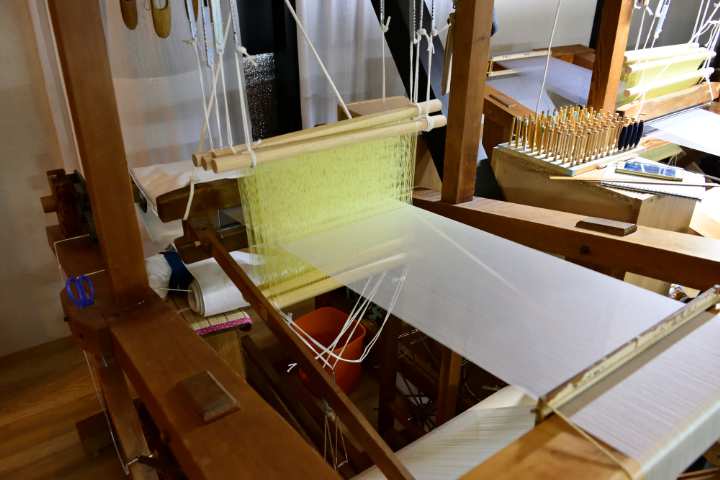
9.Handloom vs. Power Loom
Nishijin-ori can be woven by hand or by machine, depending on the complexity of the design.
The most delicate patterns are woven exclusively by hand to ensure precise detailing.
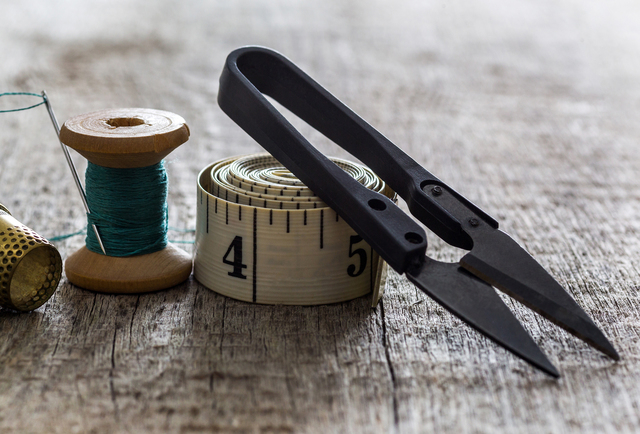
10.Velvet Cutting
For velvet Nishijin-ori, metal wires are woven into the fabric and then cut to create the signature plush texture.
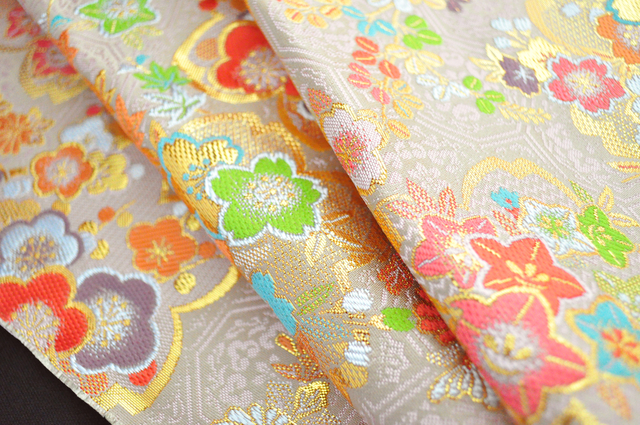
11.Finishing
Once woven, the fabric undergoes a final finishing process, ensuring it meets the highest standards of quality.